The foam manufacturing sector plays a crucial role in various industries, providing insulation, packaging, and structural components. Foam products are produced using chemical blowing agents that expand the plastic matrix during solidification. The type and quantity of blowing agent, along with processing conditions, determine the final density of the foam. Unfortunately, many of the blowing agents traditionally used in the foam industry were ozone-depleting substances with significant impacts on the climate.
To address these environmental concerns, there has been a substantial shift away from hydrochlorofluorocarbons (HCFCs) in recent years. HCFCs, once widely used as blowing agents, contribute to ozone depletion and have high global warming potentials (GWPs).
This transition to alternative blowing agents has been driven by several factors, including:
- Regulatory pressures: The Montreal Protocol and its Kigali Amendment have mandated the phase-out of HCFCs and HFCs, respectively.
- Environmental concerns: The negative impacts of HCFCs and hydrofluorocarbons (HFCs) on the ozone layer and climate change have motivated industries to seek more sustainable options.
- Technological advancements: The development of new, efficient, and cost-effective alternatives has made it possible for foam manufacturers to switch away from environmentally harmful substances.
As a result of these factors, the foam manufacturing sector has witnessed a growing trend towards the adoption of alternative blowing agents, such as:
- Hydrocarbons: These are low-GWP alternatives that have been widely used in the foam industry for many years.
- Water-blown formulations: These use water as a blowing agent, reducing the need for chemical additives.
- Supercritical carbon dioxide: This is a natural, non-toxic blowing agent with a low GWP.
- Hydrofluoroolefins (HFOs): These are a newer class of low-GWP alternatives that have gained popularity in recent years.
- Modified water-blown formulations: These combine the benefits of water-blown foams with other additives to improve foam performance.
By transitioning to these alternatives, the foam manufacturing sector is contributing to the protection of the ozone layer and mitigating climate change.
To ensure a sustainable future for the foam industry, it is crucial to focus on long-term alternatives that can effectively replace HFCs. This requires continued research and development especially for High Ambient Temperature (HAT) countries, as well as targeted technical and policy support to incentivize the adoption of these alternatives. By investing in innovative solutions and promoting a transition to low-GWP blowing agents, the foam industry can play a vital role in mitigating climate change and protecting the ozone layer.
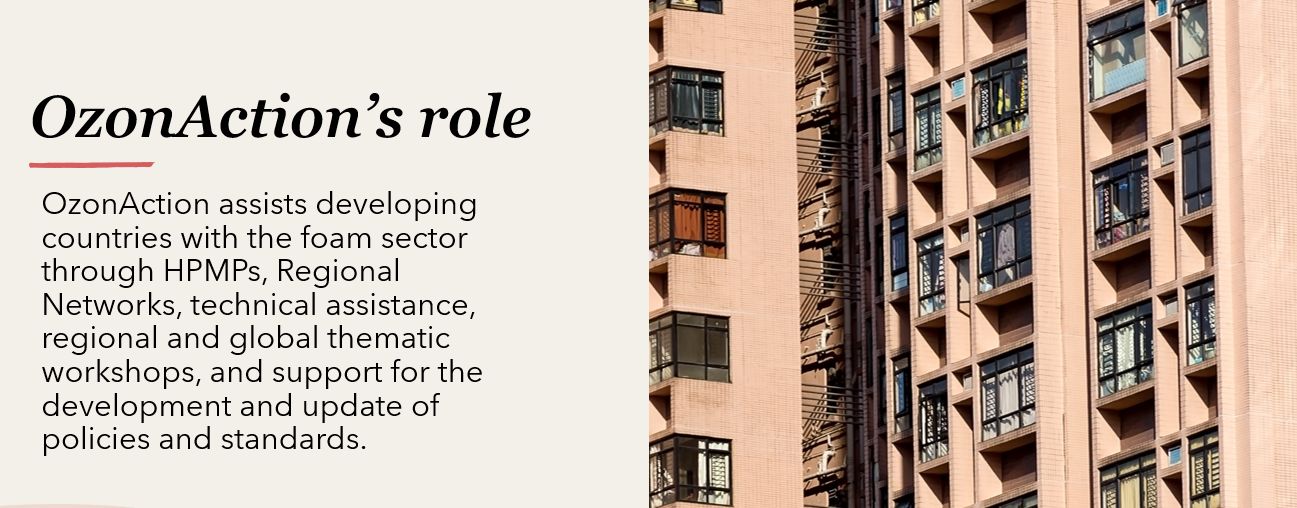
------------------------------------------------------------------
RELATED PUBLICATIONS: